
The process works by the flux in the solder. This liquid will become the circuit board's solder joints. The temperature causes the paste to melt and form a liquid. At this point, the oven's temperature rises above the solder paste's melting point. Otherwise, this can result in flux exhaustion.Īfter the thermal soak, the process reaches the reflow stage. It is, however, vital to ensure that the soak temperature is not too high. The more efficient an oven's soak phase, the less time will be necessary. The time required for a thermal soak will vary according to the board and its components. The thermal soak brings all parts up to the same heat before entering the reflow process. This stage maintains the PCB at the temperature it reached during pre-heating. In infrared ovens, the temperature should increase at a rate of 2-3 degrees per second.įollowing the pre-heating stage, the circuit board undergoes a thermal soak. It also ensures the correct and uniform heating of all parts and components. Gradually raising the temperature in a pre-heating stage ensures that the board does not sustain damage. If the pre-heating is too rapid, the board and electronic components may sustain damage. The pre-heating requires careful monitoring. The double-edged belt permits the oven to work on both sides of a circuit board.Īn important aspect of reflow soldering is the gradual ramping up of the circuit board to the temperature at which the solder will reflow. However, for larger processes, a double-sided, edge conveyor belt ensures better accuracy and efficiency. One-sided mesh conveyor belts are sometimes put to use in some reflow ovens.

Throughout the process, the circuit board will travel on the conveyor's belt. Reflow ovens solder by using multiple stages and processes along their production line. Generally, for a larger-scale process, a larger reflow oven will be necessary. Whether the processing speed is greater than the line speed will determine the size of the oven necessary. These will determine the minimum line speed of the oven as well as the repeatability of the process. The oven needs to be of a suitable size depending on the production rate and load factor. The zones enable various stages of heating and cooling all on a conveyor-type line. These ovens contain several different temperature-controlled zones. Generally speaking, reflow soldering for SMT uses infrared or convection method ovens. The reflow soldering oven is the most vital stage in the whole reflow soldering process. The Role of Ovens in the Reflow Soldering Process This allows for the secure transfer of the components to the oven. Pick and place machines allow for rapid, highly precise application of the electrical components to the circuit board in a repeatable process.įollowing placement, the natural adhesive of the solder paste temporarily holds the components in place.
#SOLDER REFLOW TEMPERATURE MANUAL#
The technology removes the need for a laborious and lengthy manual process. This requires the use of a pick and place machine. Some mass production systems utilize both a solder mask and paste machine for a more automated process.Īfter the direct application of solder to the specified areas of the board, it is time to put the components in place. (You can read more about the solder paste printing process here) It indicates the areas for solder application. The paste mask is a stencil to be placed on the PCB. In this stage, accuracy is key.įor this reason, a paste mask is essential when applying solder. The paste must be applied only to the relevant areas of the circuit board. These advances have ensured that reflow soldering can provide the highest quality soldering in the production of surface mount electronics.Īfter the printing of a circuit board, the first step in reflow soldering is the application of the solder to the board. Secondly, there have been several advances in infrared soldering processes over the years. This capacity enables extremely rapid mass production of circuit boards. Primarily, the oven method allows for a far greater soldering capacity than hand soldering. Reflow soldering is common in circuit board production for a couple of reasons. At this point, the solder sets, sealing the electrical components to the circuit board. After the oven stage, the circuit board undergoes a cooling stage. This causes the solder paste to melt (reflow). This entails that electrical components stick when placed onto the circuit board.ĭuring the reflow soldering process, the PCB passes through an oven. The process involves the application of a solder paste (composed of solder and solder flux) to the necessary areas of a circuit board.
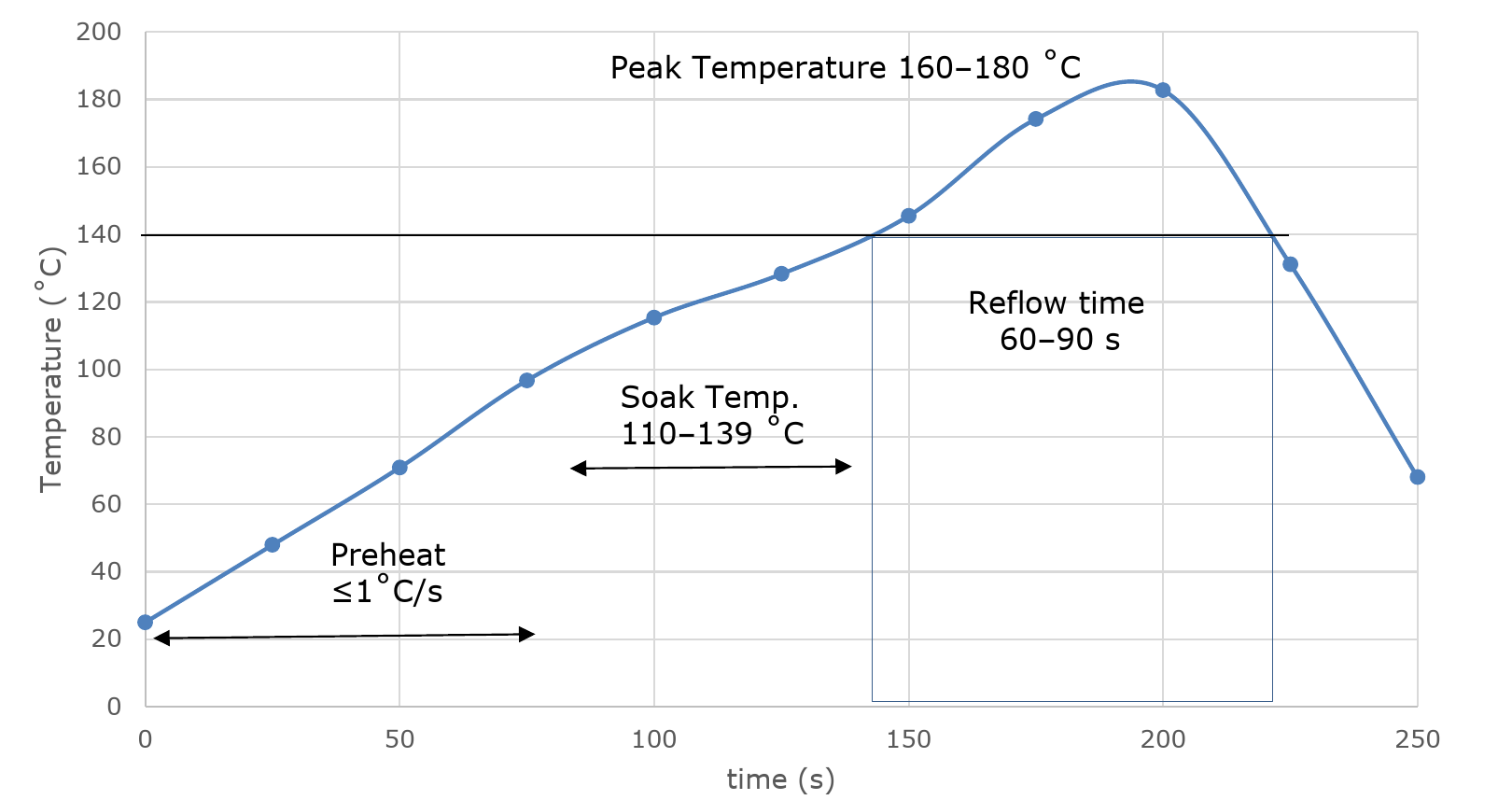
The infrared reflow soldering process is a common method for the rapid mass production of printed circuit boards (PCBs).
